感電災害に対応する感電体感ユニットの製品化が2016年にリリースされると急激に巻き込まれ災害、挟まれ災害、切創災害などの痛さを伴った体感が多く求められるようになりました。市場要求は、リアルに様々な災害対応できる触覚体感ユニットの実現でした。2014年に開発が完了していた高機能な触覚ユニット(305話参照)の量産化作業を進めます。プロトタイプ高機能触覚ユニットより利用しない幾つかの機能を取り除き、痛覚生成回路を新たに開発し追加します。後に要求が上がる力覚ユニットを駆動する機能を付加した背負い型触覚再現スーツへと発展していきます。
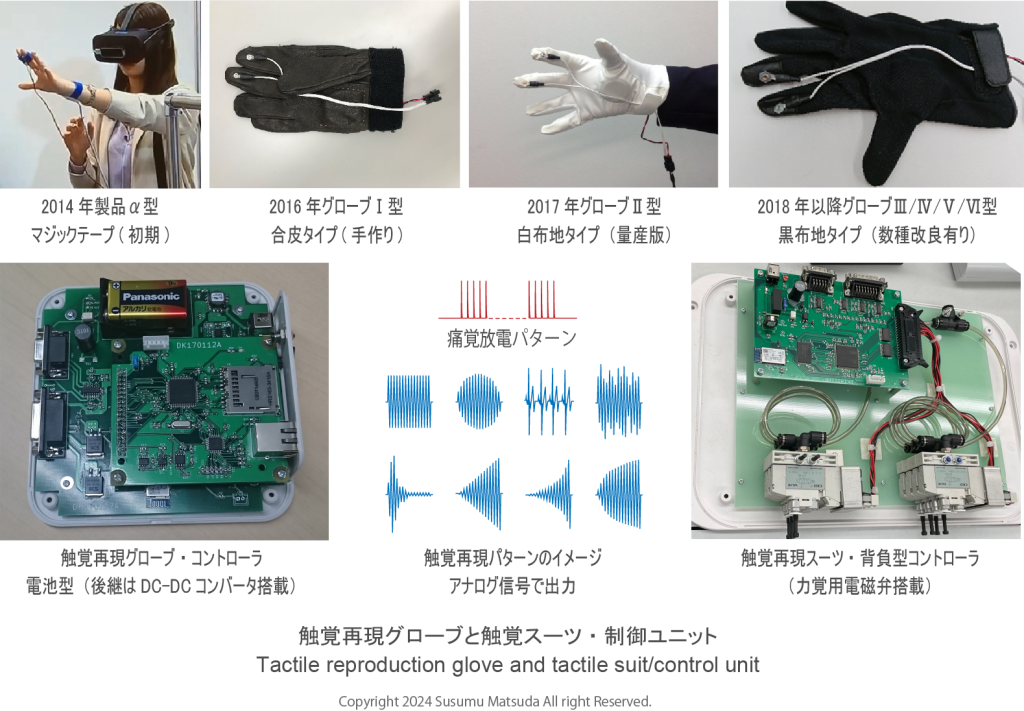
触覚再現ユニットの製品実現には、少し時間を要する課題が見つかります。痛覚放電を指先に与えると同時に手に触圧覚を伝達するモータの固定方法です。初期の2014年モデルは、マジックテープを使用しユニットを手に固定するタイプです。こちらは1人で装着する事が難しいとの事で、直ぐに改良を求められました。市販の合皮製グローブを手作りで加工し2016年に製品化します。その際に初めて皮加工の用具を使用し、学校の授業以来だった裁縫によりモータ袋を手袋内に設ける為に作業を行いました。さすがに手工業による量産は厳しいと判断します。安定した品質を保つ為に触覚用グローブの開発に取り掛かります。この段階でも課題が次々に見つかります。グローブの利用は実用化されていた指の認識率を大きく低下させる問題が発生します。必然的に画像処理が可能な布地開発へと進みます。布地の選定に始り、利用する糸の材質も問題となります。これらの課題を全て解決し布製で白地グローブを1年かがりで2017年に製品化します。白地グローブを市場に出すと、使用中汚れが気になると報告が上がってきます。衛生面でグローブを洗濯すると色落ちが起こり素材の改良要望が多く上がってきます。汚れが目立たたない洗濯可能な黒地のグローブ開発へと進みだします。その後も手の大きさに応じサイズ種類の拡大、装着性の改良、切れ難くする為の構造変更、ハードウエアの組み込み性改良等の様々な課題が上がり改良作業が進みます。現在もグローブの配線材の断線を減らす改良の検討が続いています。