Starting in 2012, we will strengthen our efforts to find applications that are effective with VR. In order to commercialize a VR killer app, we will explore the possibility and effectiveness of experiencing a disaster using VR content created as a program to overcome fear of heights. During the research activities, it became clear that falls were the most common cause of death from work-related accidents. In 2013, we developed a fall accident scenario at a work site and discovered that only 20 to 40% of people felt scared when experiencing a fall using VR (visual and auditory), according to a survey conducted after experiencing the experience. We understand. Research has shown that the experience of falling requires reproducing a sense of balance that reproduces gravity. First, we will develop a device that lowers the floor by 50mm. Later, in 2015, we developed a mechanism that automatically returns the floor to improve the experience cycle. Through numerous tests, we have discovered that reproducing the wind is important when it comes to experiencing a fall, and we have added a function that reproduces the skin sensation caused by wind pressure.
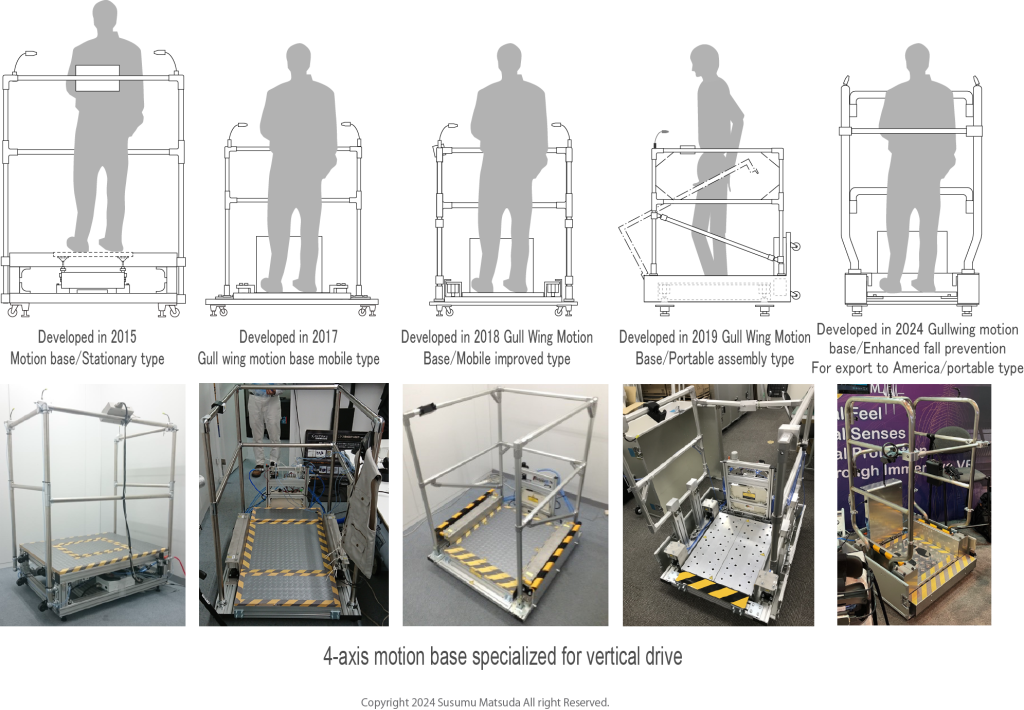
The motion base, which operates the floor in 6 degrees of freedom (6DOF), was realized in an airplane training simulator. The cost is extremely high because it is controlled by 6-axis hydraulics or servo motors to reproduce 6 degrees of freedom. Research activities revealed the need for a maintenance-free, unbreakable, low-cost motion base for use at work sites. The image on the left is an installation-type floor-driven vibration device that was commercialized in 2015. We have developed a device controlled by an industrial air cylinder so that it can be operated at work sites. Sales will begin in 2016 as a VR disaster experience system. Users are increasingly demanding smaller and more mobile shaking devices. In 2017, a gull-wing type motion base unit with a reduced floor height (Floor height 318mm⇒100mm) will be developed. After that, miniaturization including a storage case will be implemented in 2018. Demand for shortening the assembly time after moving the device has increased, and in 2019, a device that requires no tools and significantly shortens the assembly time (from 60 minutes to about 5 minutes) will be commercialized. In response to export demands, we will commercialize an export-ready model with even stronger fall prevention to suit the large bodies of overseas customers.