The railway accident response and driving training simulator we developed in 2007 was basically linked to actual equipment. Therefore, the development of products aimed at improving risk awareness by experiencing disasters was initially developed as a type that linked to actual equipment, similar to a simulator. When interlocking with actual equipment, no problems appear when contact is determined between tools and equipment using a simple simulation. However, when synthesizing the hand position in the virtual space and the handle, etc. in the real space, a mismatch in position occurs, causing a problem due to positional deviation. To prevent this, it is necessary to calibrate the coordinates of virtual space and real space. This calibration operation takes time and trouble during operation and becomes an obstacle during operation.
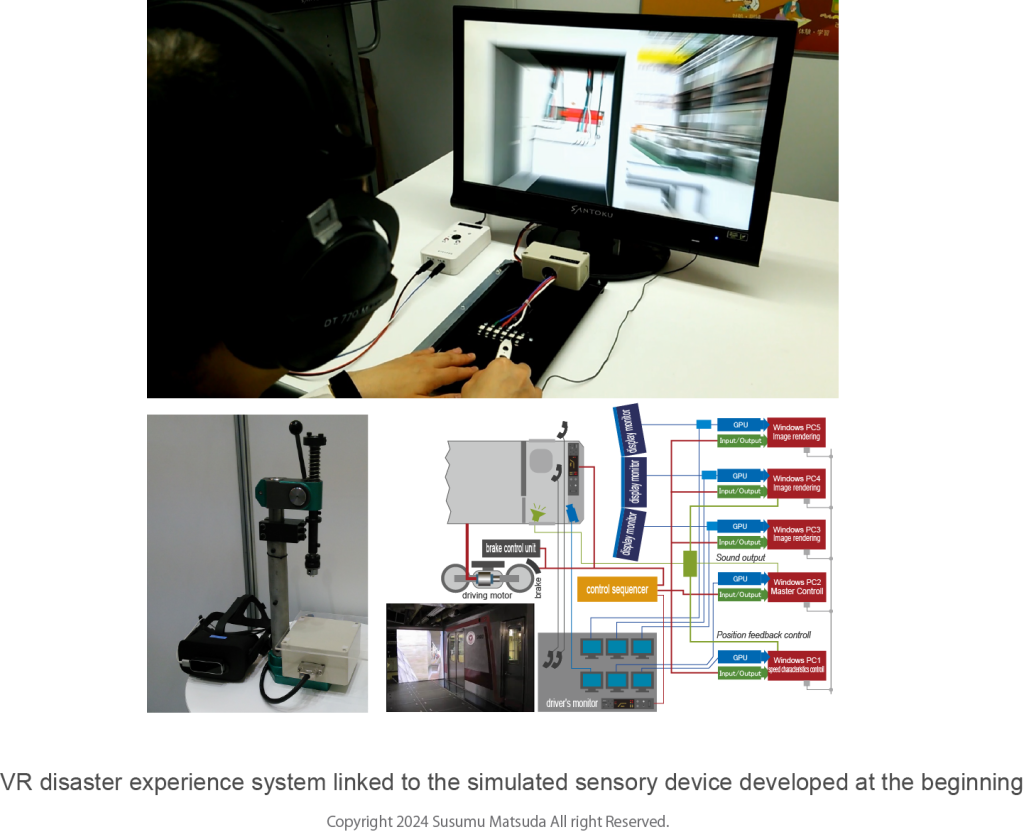
To perform spatial alignment calibration between virtual space and real space, a motion tracking device with high position detection accuracy is required. The use of high-performance motion tracking equipment is hampered by hardware costs. The low-cost marker less motion tracker that appeared in 2015 (see episode 303) had poor positioning accuracy and could not easily solve this problem. Therefore, we have given up on the experience of linking with real devices and changed our policy to reproducing the tactile sensation in a virtual space. Although a prototype of a high-performance tactile unit (see episode 305) was completed in 2014, it is hoped that a cost-effective electric shock experience unit specialized for electric shock disasters will be put into practical use. We have commercialized a low-cost electric shock experience unit that simulates the pain caused by electric shock and the numbness caused by an eccentric motor.
