Development of the motion base that generates a sense of balance began in 2014. The purpose of developing the motion base is to start developing a unit for use in training to reproduce crash and earthquake disasters and respond safely. Motion bases capable of reproducing six degrees of freedom already existed in aircraft and vehicle driving simulators. Motion bases use hydraulics and servo motors, and many large units are equipped with high-performance functions, which makes them expensive and difficult to adopt. Therefore, we aim to realize a motion base that keeps costs down even if it means limiting functions. In order to realize a unit that can move at low cost, we give up on six degrees of freedom and aim to realize a unit that is limited to four degrees of freedom of up and down movement. We began thinking about realizing a unit that would simulate the experience of vibration by installing a large vibrator under the floor, which has a simple structure. As we continued to consider it, we found that a large, high-output vibrator was needed, and a high-output control unit was also needed, which did not meet the conditions in terms of cost. If a high-output drive driver was used on four axes, we would proceed with the design work while considering the use of servo motors.
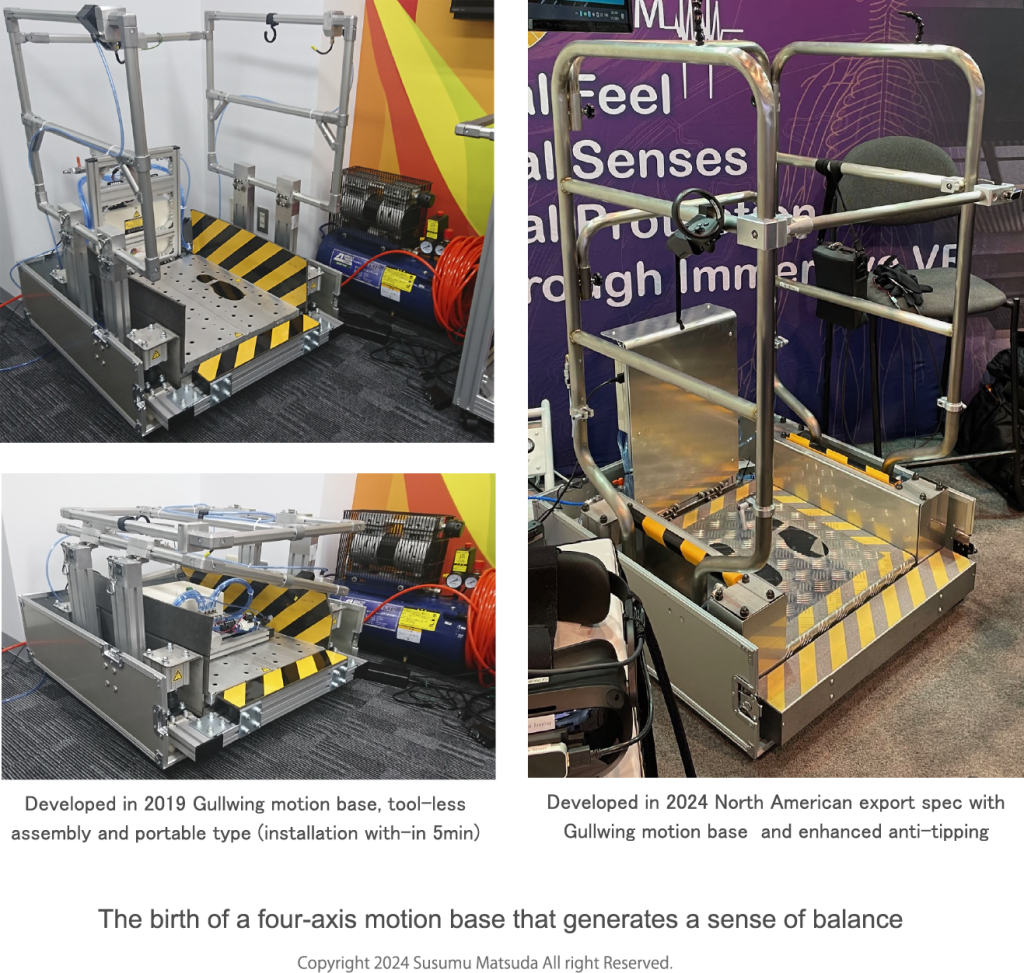
I have 13 years of experience in designing semiconductor manufacturing equipment and was familiar with the advantages and disadvantages of servo motors. As we continue to study, we find that it is difficult to operate servos in manufacturing sites where dust flies, maintenance-free operation cannot be achieved due to the failure rate of the control unit, and high-speed natural fall operation cannot be achieved, and we cannot achieve our goals. Considering the very harsh operation of manufacturing sites and the cost, we give up on the use of servo motors. We give up on the use of servo motors that we have been familiar with for many years and adopt a drive method that uses air, which has a simple structure and simple control. If it is driven by an air cylinder, the cost of the control unit can be reduced and maintenance-free for a certain period of time can be achieved. It is also possible to achieve high-speed drive and high-output drive that reproduces gravity fall. The challenge is variable drive of the operation pattern, but in order to give up high functionality and support two-speed drive, we challenged ourselves to a two-system air control method and realized a four-axis motion base with two-stage speed switching drive. We have been supplying our own units for over 10 years, while implementing design improvements for the air-driven motion base five times. In 2023, we also realized a motion base that can be used in North America. RiMM motion bases continue to be commercialized while maintaining the basic design concept.