When an electric shock experience unit was released in 2016, there was a sudden increase in demand for people to experience the painful sensations of getting caught in, being caught in, or being cut. The market demand was for a tactile experience unit that could realistically respond to various disasters. We will proceed with mass production of the highly functional tactile unit (see episode 305), whose development was completed in 2014. Several unused functions will be removed from the prototype high-performance tactile unit, and a new pain generation circuit will be developed and added. This was later developed into a backpack-type tactile reproduction suit with the added function of driving a force sensing unit, which was in high demand.
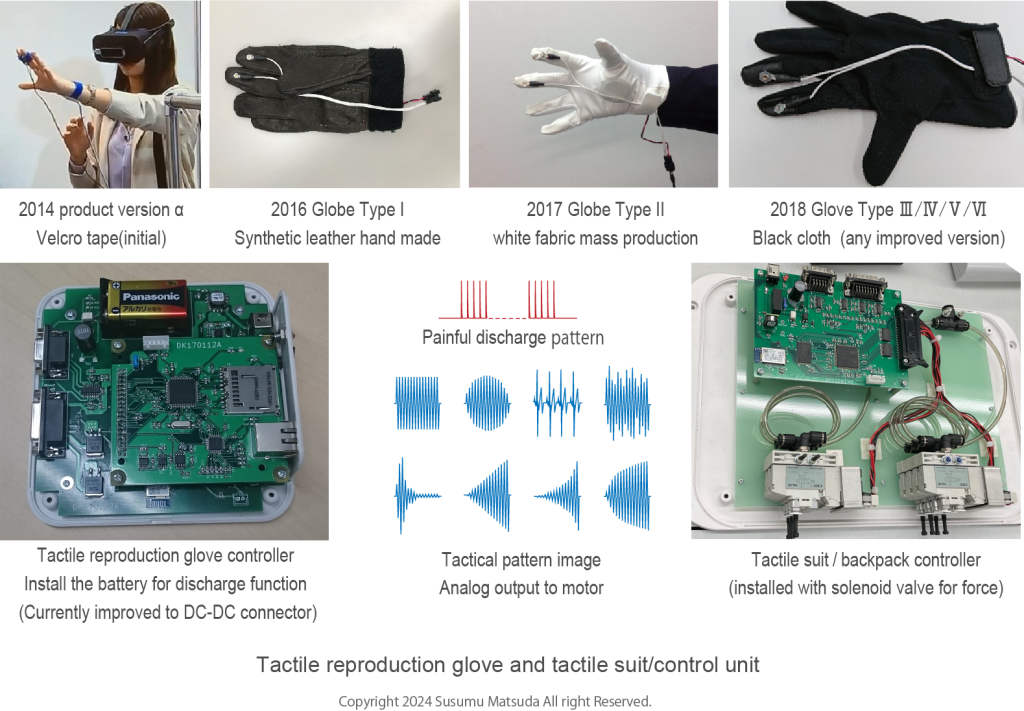
There are some issues that will take some time to realize the product of the haptic reproduction unit. This is a method of fixing a motor that delivers pain discharge to the fingertips and at the same time transmits tactile pressure sensation to the hand. The early 2014 model uses Velcro to secure the unit to your hand. This was difficult for one person to install, so improvements were immediately requested. We will hand-process commercially available synthetic leather gloves and commercialize them in 2016. At that time, I used leather processing tools for the first time, and did some sewing work requested by a school class in order to install a motor bag inside the glove. As expected, mass production by handicraft is difficult. In order to maintain stable quality, we will begin developing tactile gloves. Even at this stage, problems can be found one after another. The use of gloves poses a problem that greatly reduces the finger recognition rate that has been put into practical use. This naturally led to the development of fabrics that can be image-processed. Starting with the selection of fabric, the material of the thread used is also an issue. We will solve all of these issues and commercialize white cloth gloves in 2017, which will take one year. When white gloves are put on the market, there are reports that they get dirty during use. For hygiene reasons, when gloves are washed, their color fades and many requests are made to improve the material. We began to develop washable black gloves that didn’t show dirt. After that, various issues were raised and improvements were made, such as increasing the number of sizes depending on the size of hands, improving wearability, changing the structure to make it less likely to break, and improving the ease of incorporating hardware. Improvements to reduce disconnections in glove wiring materials are currently being considered.